Netkané textilie do interiéru a exteriéru vyrábíme pomocí moderního strojního vybavení a technologie - vpichovací linky, airlay, chemické linky, linky na povrchovou úpravu velurováním a postřihem, práškovací linka, vysekávací a formátovací stroje.
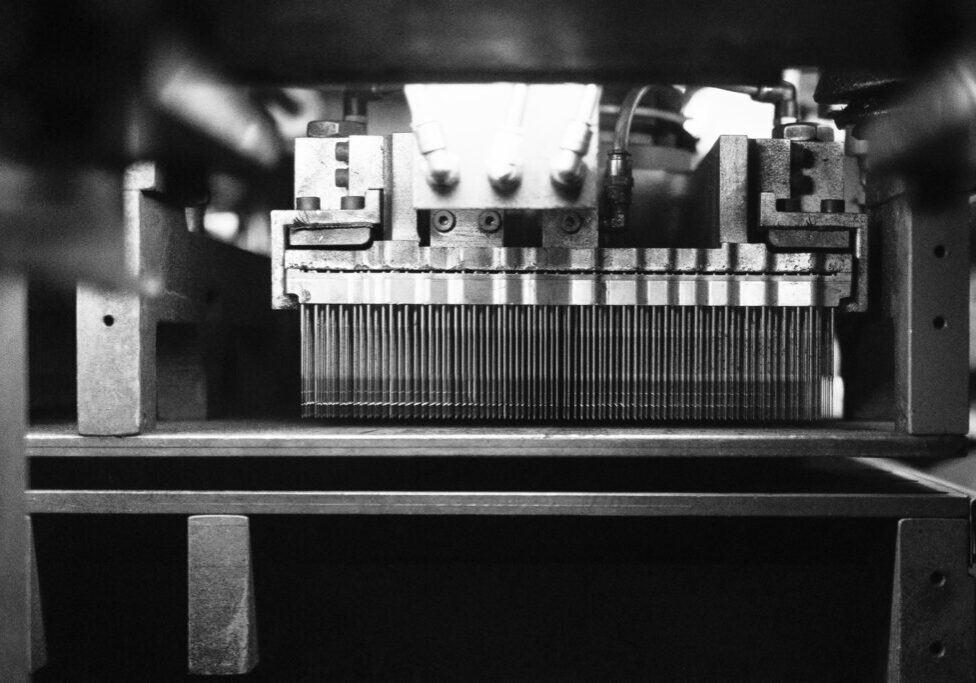
Vpichování
PRINCIP
Ze vstupního materiálu (vlákenná střiž) se mechanicky, pomocí mykacího stroje, vytvoří vrstva vláken, pavučina. Kladením několika vrstev pavučiny kladečem vzniká rouno. Rouno je následně přiváděno mezi dvě perforované desky, jejímiž otvory procházejí jehly. Ostny jehel zachycují svazky vláken, obracejí je kolmo ke směru průchodu materiálu a protahují je rounem. Při zpětném pohybu jehel se z nich vlákenné svazky vysmeknou a zaháknou na sousedních vláknech. Vlákenné rouno se vpichováním zpevňuje, ztenčuje, případně se dále spojuje s nosným podkladem (tkaninou, fólií apod.).
TECHNICKÉ PARAMETRY
Zpracovávaný materiál = PP a PES střiž, recyklovaná vlákna
Pracovní šíře = 4 - 6,5 m
VÝROBKY
Automotive
Geotextilie
Technické textilie
Airlay
PRINCIP
Technologie Airlay vytváří strukturu-textilii z náhodně orientovaných vláken vzájemně propojených pojivem. Vstupní materiály jsou promíchány v aerodynamické komoře. Následně je vzniklá vrstva ukládána na děrovaný pás a unášena do termo komory, kde vlivem tepla a tlaku horního pásu dochází k roztavení pojiva a ke stlačení vrstvy na požadovanou tloušťku. Vzniklá textilie je na konci linky formátována do tvaru desek, nebo rolí.
TECHNICKÉ PARAMETRY
Zpracovávaný materiál = polyesterová vlákna – PES, polypropylenová vlákna – PP, směsi syntetických a přírodních vláken, recyklovaná vlákna – přírodní a syntetická vlákna a recyklované textilie
Plošné hmotnosti = 600 – 6000 g/m2
Tloušťka výrobku = 5 – 200 mm
VÝROBKY
Zelené střechy
Automotive
Izolace
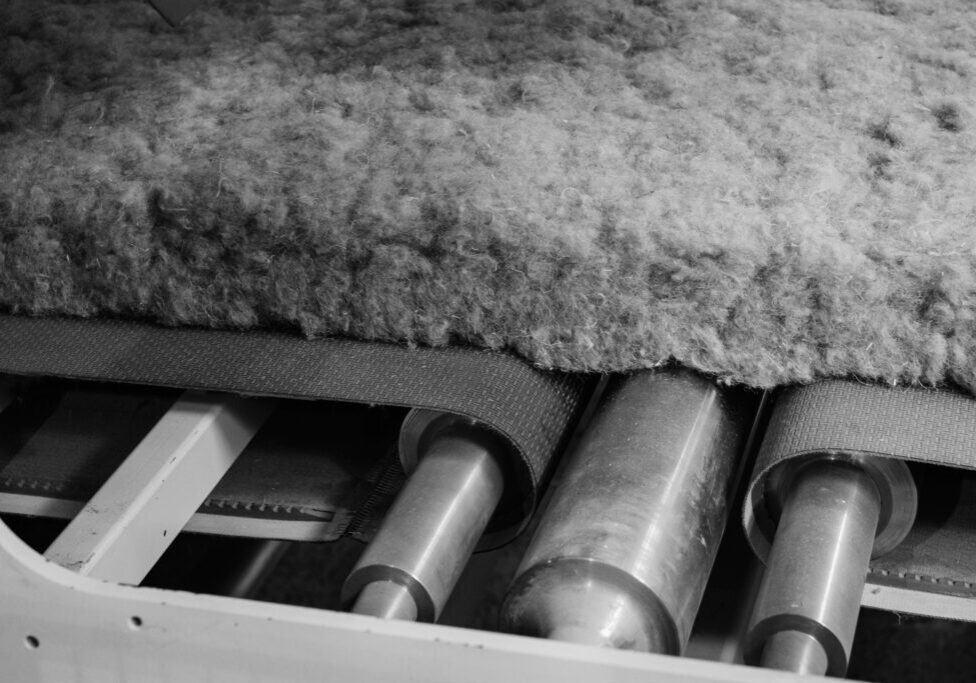

Impregnace pěnou
PRINCIP
Chemická úprava netkaných textilií pro zpevnění vlákenné vrstvy nebo pro dosažení požadované vlastnosti textilie. Samotná úprava se provádí impregnací-nánosem zpěněného pojiva a úpravy do struktury textilie. Pěna může být nanášena na jednu, nebo na obě textilie. V případě nanášení pěny z obou stran je možné použít na každou stranu jiné pojivo nebo úpravu. Proces impregnace je ukončen v teplovzdušné komoře, ve které jsou nanesené pojivo a úprava aktivovány. Po zchlazení je textilie naformátována do požadované šíře a tvaru, do dílce nebo role.
ZPRACOVÁVANÉ MATERIÁLY
Netkané vpichované textilie
Latexová pojiva
FUNKCE ÚPRAV
Nehořlavá
Zpomalení hoření
Odolnost vůči suchým zipům
Zpevnění vrstvy vláken
VÝROBKY
Automotive
Technické textilie
Práškování
PRINCIP
Chemická úprava netkaných textilií pro zpevnění vlákenné vrstvy, pro nános lepivé vrstvy nebo pro spojení dvou materiálů pomocí nánosu termoplastického práškového pojiva. K aktivaci pojiva dochází v teplovzdušné komoře. Po následném zchlazení je textilie naformátována do požadované šíře a tvaru, nařezána na formáty nebo navinuta do rolí.
ZPRACOVÁVANÉ MATERIÁLY
Netkaná textilie
Práškové pojivo LDPE nebo HDPE
PE fólie
VÝROBKY
Automotive
Technické textilie
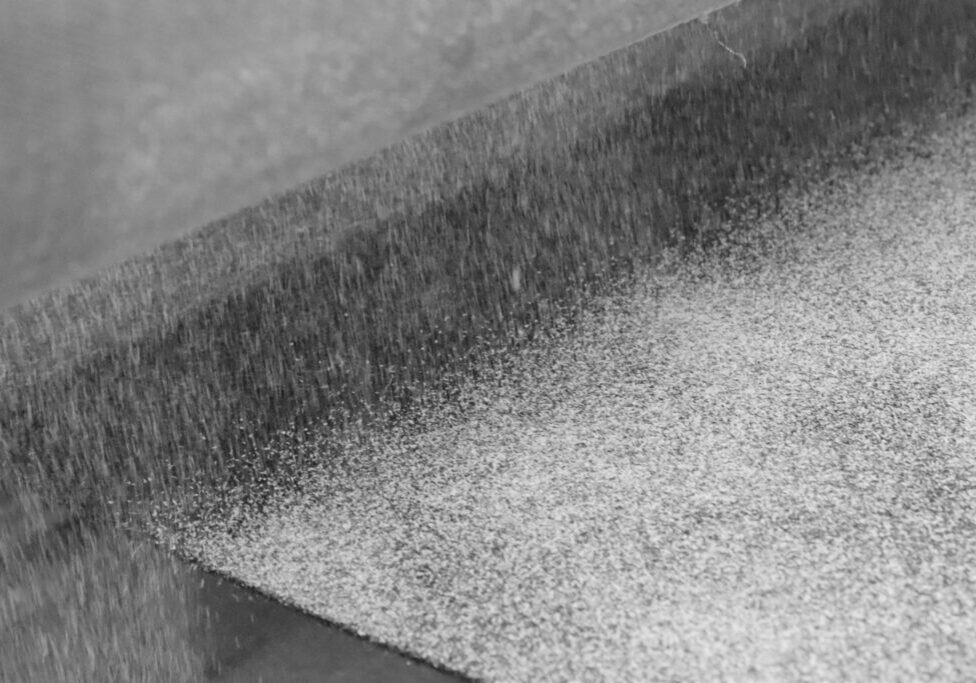
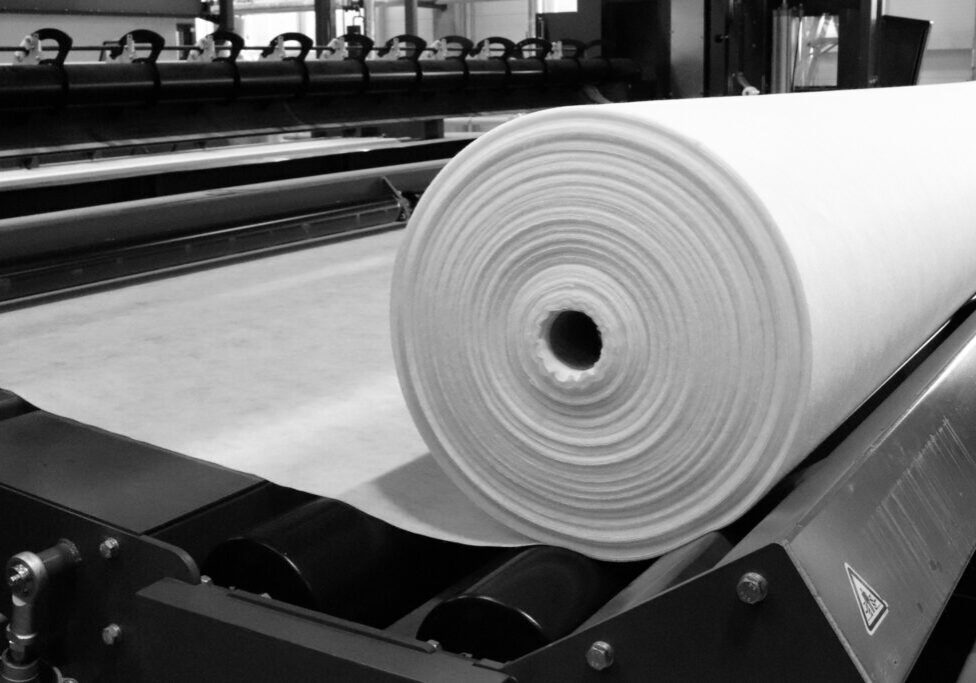
Kalandrování
PRINCIP
Zpevnění netkané textilie vlivem tepla a tlaku, kdy k samotnému zpevnění dochází ve štěrbině mezi dvěma válci, ohřátím a stlačením netkané textilie. Ohřátím dojde ke změkčení vláken a vlivem tlaku pak ke vzniku pojících míst mezi vlákny. Následným zchlazením se spojení zpevní.
ZPRACOVÁVANÉ MATERIÁLY
Netkaná vpichované textilie
VÝROBKY
Geotextilie
Technické textilie
Velurování a postřih
PRINCIP
Mechanické úpravy netkaných vpichovaných textilií, při kterých je docilováno rovnoměrného povrchu, textilii je dodáván vzhled veluru nebo semiše. Charakteristickými rysy takových výrobků jsou jejich jemný pocit a sametový povrch.
ZPRACOVÁVANÉ MATERIÁLY
Netkané vpichované textilie
VÝROBKY
Automotive
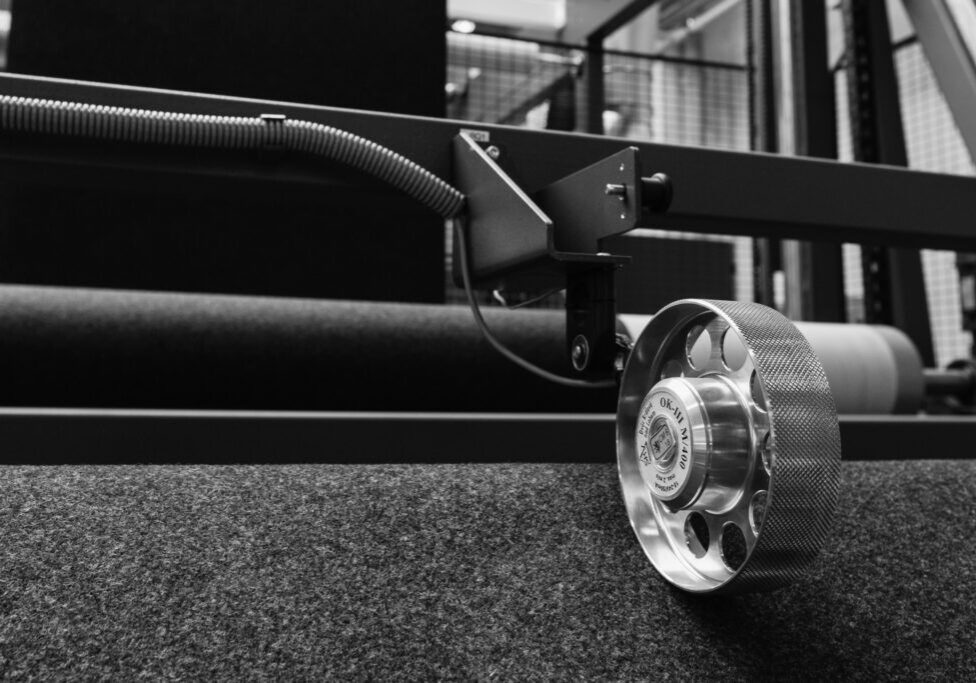
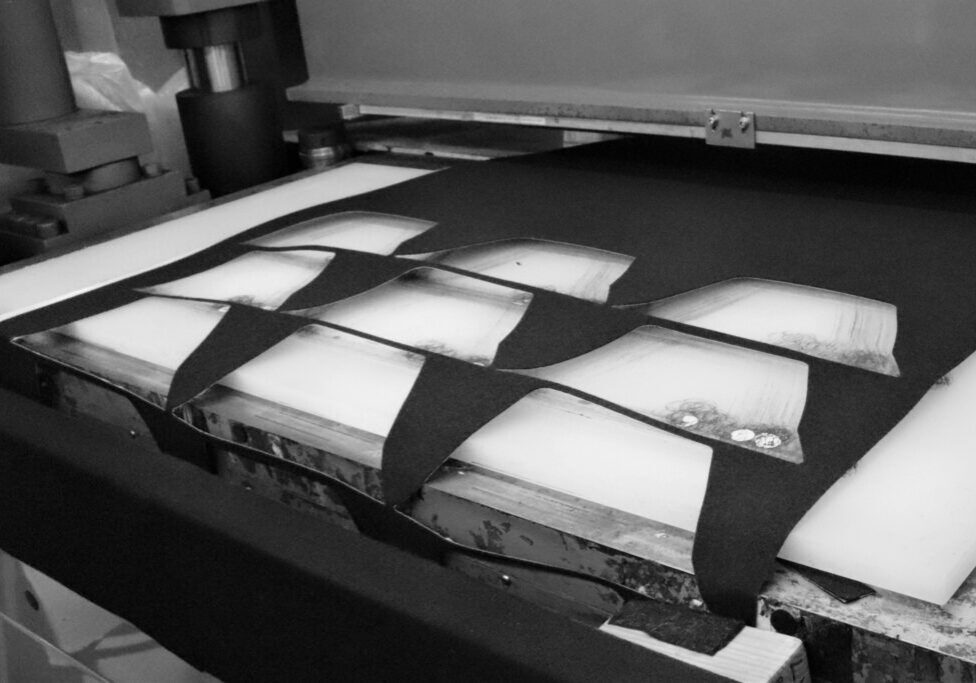
Vysekávání a řezání
PRINCIP
Úprava rozměrů netkané textilie na řezacím stroji, nebo výroba dílců požadovaného tvaru na pneumatickém lisu nebo plotru.
ZPRACOVÁVANÉ MATERIÁLY
Netkaná vpichované textilie
Airlay textilie
VÝROBKY
Automotive
Izolace
Technické textilie
CERTIFIKACE
Výrobky pravidelně testujeme jak u nás, tak i v nezávislých laboratořích. Kvalitu našich materiálů rovněž zajišťuje vyspělý systém kontrol. Systém řízení jakosti je v RETEXu certifikován podle norem
ISO 9001, ISO 14001, IATF 16949, ISO 45001, ISO 50001, OEKO – TEX Standard 100 a IRIS Certification® Conformity assessment:2020 and based on ISO/22163:2023
Naše textilie také úspěšně procházejí řadou zákaznických auditů.